Разработка грунта погрузчиками
В зависимости от мощности и грузоподъемности погрузчиков, физико-механических свойств разрабатываемых грунтов ковш погрузчика можно наполнять раздельным, совмещенным, экскавационным и комбинированным способами.
При раздельном способе (рис.1, а) ковш устанавливают режущей кромкой горизонтально или под углом 3 - 5°. При движении со скоростью. 1,4 ... 1,8 км/ч ковш внедряют в грунт на глубину 0,85 ... 1 длины ковша. После внедрения ковша и остановки машины его запрокладывают до упора и поднимают стрелу в транспортное положение. При высокой квалификации машиниста процесс подъема стрелы в транспортное положение и движения к месту разгрузки можно совместить. Во избежание ударных нагрузок на конструкции и большого износа шин не рекомендуется превышать скорость движения свыше 4 км/ч. Кроме того, для погрузчиков грузоподъемностью до 6 т нежелательно производить слишком глубокое внедрение ковша, так как происходит перенапряжение гидросистемы подъема стрелы. Этот способ наиболее широко применим при погрузке сыпучих строительных материалов.
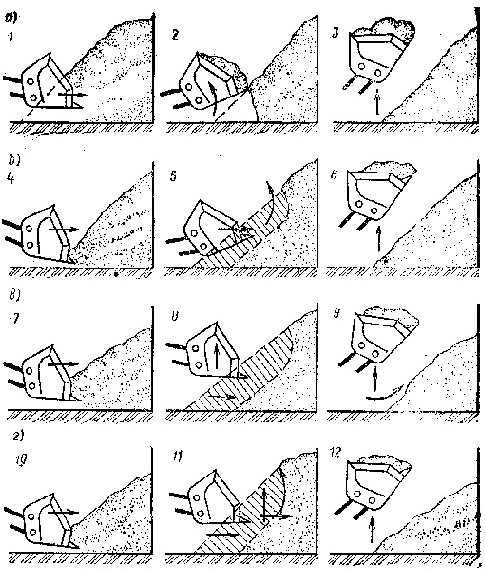
Рис.1. Основные схемы разработки грунта погрузчиками
а - раздельный; б - совмещенный; в - экскавационный; г - комбинированный; 1, 4, 7, 10 - внедрение ковша; 2 - запрокидывание и поворот ковша; 3, 6, 12 - подъем стрелы для установки ковша в транспортное положение; 5, 8 - поворот ковша с одновременным продвижением вперед; 9 - подъем ковша и подъем (опускание) опускание стрелы для установки ковша в транспортное положение; 11 - попеременный поворот ковша и подъем стрелы с одновременным движением вперед
При совмещенном способе (рис.1, б) внедрение ковша в грунт происходит на глубину 0,5 ... 0,6 длины ковша, при скорости 2,5 ... 5 км/ч ковш запрокидывают постепенно. Для наилучшего заполнения ковша необходимо, чтобы скорость движения погрузчика была близка к средней линейной скорости запрокидывания режущей кромки ковша. Тогда напорное усилие внедрения снижается в 2 - 3 раза по сравнению с раздельным способом. Данный способ копания наиболее эффективен для погрузчиков грузоподъемностью до 10 т при разработке грунтов I - II групп из целика и в разрыхленном состоянии, а также погрузке строительных материалов.
Экскавационный способ (рис.1, в) заключается в том, что ковш наклоняют к основанию забоя на угол 3 - 5°. После внедрения ковша на глубину до 0,4 - 0,5 глубины ковша производят подъем стрелы. При выходе из забоя во избежание потерь грунта ковш запрокидывают. При разработке тяжелых грунтов, когда не обеспечивается необходимая глубина внедрения, следует производить дополнительные внедрения. Этот способ целесообразен при разработке плотного и связного грунта при высоте забоя 1,5 м и выше.
Для погрузчиков грузоподъемностью более 10 т максимальное наполнение ковша, в особенности на грунтах IV - V групп, достигается при комбинированном способе разработки (рис.1, г). По мере внедрения котла с наклоном днища 3 ... 5° одновременно с напорным движением погрузчика с помощью механизмов поворота ковша и подъема стрелы осуществляют попеременно поворот котла на угол 2 … 3° и подъем стрелы на 5 ... 10° до момента выхода ковша из забоя. Такой способ из-за сложности применяют пока только высококвалифицированные машинисты. При этом производительность погрузчика повышается на 5 ... 10 %.
Основные способы разгрузки ковша
Большинство отечественных (ТО-30, ТО-28, ТО-25А) и ряд зарубежных погрузчиков разгружаются запрокидыванием ковша до максимального положения, поднятием стрелы на необходимую высоту и последующим опорожнением ковша (после подачи к автотранспорту).У погрузчиков ТО-21-1А, ТО-18А и др. в процессе подъема стрелы ковш автоматически из максимально запрокинутого положения выходит в положение разгрузки. После разгрузки ковш устанавливается в положение копания без вмешательства машиниста.
Ковш можно разгружать двумя способами. При первом способе стрелу поднимают на высоту, достаточную для поворота ковша, а при втором - стрелу поднимают на высоту кузова самосвала так, чтобы зубья ковша находились примерно в центре кузова. Затем ковш поворачивают при незначительном подъеме стрелы. При этом высота разгрузки существенно зависит от угла поворота коша в момент его полного опорожнения.
При втором способе минимально необходимая высота разгрузки меньше на 8 ... 10 %, что значительно влияет на эффективность использования погрузчика в стесненных условиях. Однако при этом продолжительность разгрузки ковша на 30 ... 40 % больше.
Технологические схемы работы погрузчиков
Схема работы зависит от типа погрузчика. Для фронтальных погрузчиков на пневмоколесном ходу (рис.2) наиболее распространена схема с частичным разворотом погрузчика на различные углы при отходе от забоя. Загружаемые самосвалы при этом устанавливают параллельно или под нужным углом к фронту забоя.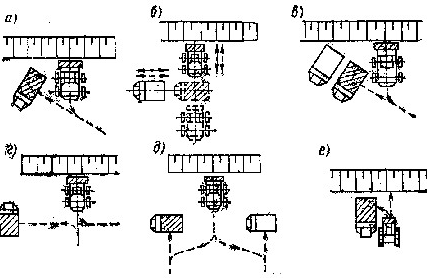
Рис.2. Основные схемы работы погрузчиков в комплекте с автосамосвалами
а, в, - с поворотом на 40 - 50°; б - челночным способом; г - с поворотом на 90°; д - при спаренной установке транспортных средств; е - челночным способом с разгрузкой в сторону
При работе гусеничных и мощных пневмоколесных погрузчиков рациональной является челночная схема работы, когда погрузчик перемещается вперед и на зад на расстояние 10...20 м перпендикулярно фронту забоя без разворотов. При этом самосвал также совершает челночные движения параллельно фронту забоя на расстояние, достаточное для проезда погрузчика.
Минимальная дальность транспортировки (до 10 м) обеспечивается при работе полуповоротных погрузчиков. Благодаря возможности поворота рабочего оборудования в плане до 90° самосвалы можно устанавливать под различными углами к фронту забоя.
Эффективная работа погрузчиков при погрузке грунта в самосвалы обеспечивается при следующих соотношениях грузоподъемности, т:
Таблица 1
Соотношение грузоподъёмности погрузчика и самосвала
грузоподъёмность погрузчика | 2 | 3 | 4…6 | 10…15 |
грузоподъёмность самосвала | 7…10 | 10…12 | 15…27 | 27…40 |
Одноковшовые погрузчики используют последующим технологическим схемам:
1. Схема "Выемка - транспортировка" наиболее приемлема для разработки грунтов I и II групп, реже - III группы. В этом случае используют основной ковш, хотя на мощных погрузчиках (L-34, ТО-21-1А и др.) можно устанавливать и увеличенные ковши. На грунтах III - IV групп в течение непродолжительного времени могут быть применены погрузчики с уменьшенным ковшом, а также основной ковш с неполным его заполнением. Грунт разрабатывают тонкой стружкой экскавационным или комбинированным способом. Данная схема особенно эффективна в транспортном или гидротехническом строительстве (сооружение на сыпей и выемок, плотин и дамб).
2. Схема "Выемка - временное складирование - транспортировка" наиболее широко применима при планировке площадок и рекультивации земель, складирование грунта для обратной засыпки и т. д.
З. Схема "Рыхление - выемка - транспортировка" используется после предварительного рыхления грунтов IV - V групп. В этом случае могут быть применены погрузчики грузоподъемностью З т (ТО-25А, ТО-18А и др.), оборудованные основным или уменьшенным ковшом.
Степень рыхления грунтов увеличивается при их последующем перелопачивании и складировании экскаваторами или бульдозерами. Поэтому при работе по схеме "Рыхление - временное складирование - выемка - транспортировка" на разработке предварительно разрыхленных грунтов III - V групп используют даже легкие погрузчики грузоподъемностью меньше 2 т (ТО-30 и др.).
С целью определения технической производительности погрузчиков различных типов были проведены хронометражные и тензометрические замеры продолжительности выполнения погрузчиком технологического цикла по отдельным элементам. При разработке грунтов I группы с погрузкой в самосвалы наиболее распространенной является схема с поворотом погрузчиков. При этом средняя дальность транспортировки грунта для строительных погрузчиков составляет 30-40 м (табл. 2).
Таблица 2
Техническая производительность одноковшовых погрузчиков при разработке грунта I группы
Показатель | Погрузчик | ||||||||
ТО-6А | ТО-30 | ТО-25А | ТО-18А | ТО-27 | ТО-21-1 | UN-050 | UNS-151 | L-34 | |
Дальность транспортировки, м | 40 | 40 | 40 | 20 | 40 | 80 | 35 | 35 | 40 |
Продолжительность, с | |||||||||
копания | 6 | 6 | 7 | 6 | 6 | 8 | 3 | 8 | 6 |
транспортировки | 26 | 24 | 30 | 23 | 34 | 31 | 27 | 31 | 31 |
разгрузки | 4 | 4 | 3 | 3 | 5 | 10 | 3 | 4 | 5 |
холостого хода | 21 | 20 | 22 | 20 | 31 | 23 | 21 | 22 | 29 |
цикла | 57 | 54 | 62 | 52 | 76 | 72 | 54 | 65 | 71 |
Коэффициент наполнения ковша Кн | 0,7 | 0,75 | 1 | 1,1 | 1,1 | 1,1 | 1 | 0,9 | 1,1 |
Техническая производительность, м³/ч | 38,4 | 43,5 | 76 | 100 | 125 | 359 | 70 | 68 | 200 |
Эксплуатационная производительность погрузчиков Пз существенно зависит от дальности транспортировки грунтов Lтр; максимальное значение Пз при Lтр до 30 м, а при Lтр = 250 м она снижается в среднем в 4 раза.
Для повышения транспортной скорости перед началом работ необходимо спланировать и выровнить площадку, на которой будет работать погрузчик. Это значительно уменьшает потери материала из ковша при транспортировке его к месту выгрузки, повышает износостойкость шин и безопасность движения машины при высокой скорости. Обычно погрузчики транспортируют грунт на расстояние до 150... 180 м.
Одним из направлений повышения производительности погрузчиков является совмещение операций рабочего цикла, что позволяет до 1,5...2 раза сократить время цикла.
При разработке влажных, особенно связных грунтов, в котловане или в условиях карьера после завершения разгрузки в ковше может задерживаться до 25 % первоначально набранного грунта, что резко снижает эффективность работы погрузчика. С целью уст ранения отмеченного недостатка испытан ковш с принудительной разгрузкой, полная очистка которого достигается с помощью подвижной заслонки.
Землеройно-транспортные машины (ЗТМ)
К землеройно-транспортным относят строительные машины, которые за счет тягового ‚ производят послойное отделение грунта от массива и транспортируют его к месту укладки в процессе собственного перемещения. Такими машинами являются бульдозеры, скреперы и автогрейдеры (грейдеры). Исключение составляют грейдеры-элеваторы, у которых грунт транспортируется и отсыпается в отвал или транспортное средство специальным транспортирующим органом одновременно с разработкой.Бульдозеры, скреперы и автогрейдеры - это машины циклического действия. Основные операции цикла: отделение грунта от массива (копание); транспортирование его к месту укладки (отсыпки); разгрузка; возвращение машины в исходное положение. Для отделения грунта от массива используют рабочие органы ножевого типа с гладкой или оснащенной зубьями режущей кромкой. Срезанный грунт накапливается перед рабочим органом (отвалом) или поступает в ковш, которым и транспортируется к месту отсыпки. При транспортировании грунта сопротивление перемещению машины ниже, чем при копании, поэтому скорость передвижения машин увеличивается.
3емлеройно машины наиболее эффективны на массовых разработках грунтов. При разработке грунта, бульдозерами с перемещением на 50-100 м производительность машины составляет 6-76 тыс м³/год. при удельном расходе энергии 1,6-2,4 кВт*ч/м³ Производительность скреперов при дальности транспортирования 0,5 - 1,5 км в среднем 5 - 40 тыс. м³/год, удельный расход энергии 6-3,2 кВт*ч/м³.
По этим показателям ЗТМ не уступают самой дешевой экскаваторной разработке грунта с транспортированием по железной дороге.
Бульдозеры
Составляют основу парка машин в строительстве и горнодобывающей промышленности. На их долю приходится более 40% выполняемых земляных работ в стране и до 90 % вскрышных работ.Бульдозеры предназначены для послойной разработки грунтов I -III11 и частично IV групп без предварительного рыхления, плотных, прочных и мерзлых грунтов после предварительного рыхления с последующим перемещением перед рабочим органом (отвалом) на расстояние до 100 м. Их применяют при сооружении на сыпей и выемок, обратной засыпке траншей и котлованов, предварительной планировке поверхности, разравнивании грунтовых отвалов, выполнении подготовительных работ при валке отдельных деревьев, резке кустарника, корчевке пней, вскрышных работах в качестве толкачей при работе скреперов. Их широкому распространению способствует высокая производительность, универсальность, маневренность, мобильность, автономность, простота конструкции рабочего оборудования и надежность в эксплуатации.
Индексация бульдозеров имеет буквенную и цифровую части, например: Д3-42, ДЗ-170.1 и т. д. Буквенная часть отражает принадлежность бульдозеров к классу землеройно-транспортных машин, а цифровая часть - номер изделия по журналу регистрации (цифра 42 в первом случае) или указывает на связь с моделью базового трактора (базовый трактор Т-170.01 во втором случае).
Бульдозеры классифицируют по номинальному тяговому усилию, ходовым системам базовых машин, назначению и конструктивным особенностям рабочего оборудования.
Основным классификационным признаком, связанным с массой трактора и определяющим технико-экономические показатели бульдозеров, является номинальное тяговое усилие. По ному параметру бульдозеры делят на очень легкие (номинально тяговое усилие до 25 кН), легкие (25-135 кН), средние (135-200 кН), тяжелые (200-350 кН), сверхтяжелые (свыше 350 кН).
По типу ходовой системы базового трактора различают бульдозеры гусеничные и пневмоколесные. Преимущественное распространение получили гусеничные бульдозеры благодаря низкому удельному давлению на, грунт в сочетании с реализацией значительных тяговых усилий и высоких сцепных свойств гусеничных ходовых систем. Колесные машины получили преимущественное распространение там, где определяющим в работе является высокая транспортная скорость и мобильность.
Различают бульдозеры общего, специального и многоцелевого назначения. Бульдозеры общего назначения применяют для землеройно-транспортных и планировочных работ в различных грунтовых условиях в интервале температур окружающего воздуха от +40 до -40 °С.
Бульдозеры специального назначения выполняют узкоспециализированные работы: чистка снега, разработка сыпучих материалов, подземные и подводные работы, работы в зоне заражения химическими и радиоактивными отходами, при высокой (до +60°С) и низкой (до -60°С) температуре. Такие бульдозеры существенно отличаются от бульдозеров общего назначения со ставом рабочего оборудования, системой управления, тепло- и звукоизоляцией и герметичностью кабины управления.
Бульдозеры многоцелевого назначения наряду с землеройно - транспортными работами при соответствующем дооборудовании рыхлят плотные, прочные и мерзлые грунты (при установке рыхлительного оборудования), отрывают узкопрофильные траншеи (при оборудования дисковой фрезой и т. д.).
По способу установки рабочего органа (отвала) различают бульдозеры с неповоротным и поворотным отвалом. Неповоротный отвал устанавливают перпендикулярно к оси машины, поворотный - под углом к продольной оси машины, причем угол установки может иметь фиксированные значения (при ручном способе) или изменяться от 0° до максимального значения (при гидравлическом изменении положения отвала).
По типу рабочего органа (отвала) различают бульдозеры с прямым, полусферическим, сферическим и специальным (для сыпучих материалов, с толкающей плитой, с амортизаторами и т. д.) отвалом.
По приводу рабочего оборудования различают бульдозеры с гидравлическим и механическим приводом. Практически все современные бульдозеры оснащены гидравлическим приводом рабочего оборудования.
Бульдозеры с неповоротным отвалом (рис.3) агрегатируют с гусеничными тракторами 4 всех известных тяговых классов. Бульдозерное оборудование включает отвал 1, толкающие брусья 5, гидрораскос 2 и гидроцилиндры 3 привода рабочего оборудования.
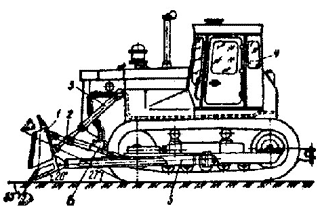
Рис.3. Бульдозер с неповоротным отвалом
1 - отвал; 2 - гидравлический раскос; 3 - гидроцилиндры подъема; 4 - базовый трактор; 5 - толкающий брус; 6 - гибкие рукава
На неповоротных бульдозерах устанавливают прямые, полусферические и сферические отвалы, а также специальные.
Неповоротные отвалы легких и средних бульдозеров выполнены из лобового листа криволинейной формы, усиленного с тыльной стороны продольными верхней и нижней коробками жесткости и вертикальными ребрами жесткости, неповоротные отвалы тяжелых бульдозеров коробчатого сечения. Козырек в верхней части отвала предотвращает пересыпание грунта через верхнюю кромку. В нижней усиленной части отвала предусмотрен ряд отверстий для крепления средних и крайних ножей. Боковые пластины отвала имеют отверстия для установки уширителей.
Толкающие брусья передают тяговое усилие от базового трактора на отвал. У них коробчатое сечение, они могут быть прикреплены к отвалу жестко (бульдозер ДЗ-42), шарнирно (все отвалы без перекоса), универсальными шарнирами или крестовинами (отвалы с гидроперекосом). К раме гусеничной тележки толкающие брусья крепятся при помощи шаровой опоры.
Между толкающими брусьями и верхней частью отвала устанавливают винтовые или гидравлические раскосы, с помощью которых регулируют угол резания (+-5) и симметричный перекос (+-16), а также систему горизонтальных тяг, соединенных в середине тыльной части отвала механизмом компенсации перекоса. Раскосы и система горизонтальных тяг обеспечивают необходимую продольную и поперечную жесткость рабочего оборудования при воздействии сил сопротивления копанию.
Гидрораскосы снабжены двухсторонними гидрозамками, исключающими самопроизвольное изменение конфигурации рабочего оборудования под действием внешних нагрузок.
Поднимают и опускают рабочее оборудование гидроцилиндрами, что позволяет использовать часть массы машины при заглублении отвала, особенно при разработке плотных грунтов.
Бульдозеры с поворотным отвалом (рис. 4) монтируют гусеничные тракторы 1 тягового класса до 35-го. Бульдозерное оборудование (рис. 4, а) состоит из отвала 4, универсально толкающей рамы 3, толкателей 6, раскосов 5 и гидроцилиндров 2 подъема и опускания отвала.
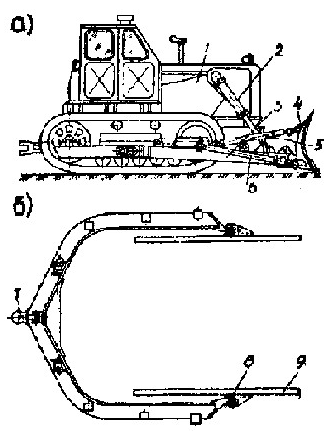
Рис.4. Бульдозер с поворотным отвалом
а - общий вид; б - универсальная рама; 1 - базовый трактор; 2 - гидроцилиндры привода отвала; 3 - универсальная рама; 4 - отвал; 5 - винтовой раскос; 6 - толкатель; 7 - паровая опора; 8 - проушина для крепления к ходовой тележке трактора; 9 - рама гусеничной тележки
Отвал по конструкции аналогичен отвалу неповоротного бульдозера, но в центре с тыльной стороны расположена пята для соединения с шаровой опорой 7 универсальной толкающей рамы. Поворотный отвал имеет меньшую высоту и применяется преимущественно для выполнения планировочных работ и обратной засыпки траншей. Бульдозер с повернутым в плане отвалом может двигаться вдоль траншеи, при этом грунт перемещается вдоль отвала и ссыпается в траншею.
Универсальная толкающая рама (рис. 4, б) имеет в плане вид арки, в передней части которой приварена шаровая опора, а концы ее шарнирно 8 связаны с рамами гусеничных тележек трактора 9.
Отвал с плане фиксируется двумя боковыми толкателями каждый из которых состоит из упорного бруса и винтового раскоса, связанных шарнирно. Передние концы брусьев и раскосов крестовинами соединены с отвалом. Задняя часть толкателей шкворнями крепится в отверстиях кронштейнов верхней части универсальной рамы. Угол установки отвала в плане изменяют путем перестановки упоров толкателей в соответствующие кронштейны. Угол поворота составляет 25-27° в каждую сторону.
Основными направлениями совершенствования бульдозеров являются расширение типоразмерных рядов (от мини-бульдозеров до машин большой единичной мощности); унификация оборудования; переход к блочно-модульному принципу компоновки оборудования; широкое применение гидропривода не только в управлении рабочим оборудованием, но и в трансмиссии базовых машин; разработка и применение рабочих органов интенсифицирующего действия; полная гидрофикация управления рабочим, оборудованием (изменение угла резания, угла перекоса отвала, угла в плане, смещение отвала вбок и т. д.); внедрение систем автоматического регулирования режимов работы по оптимальному значению силы тяги и по положению рабочего органа при выполнении операций технологического цикла; повышение эксплуатационной экономичности бульдозеров; улучшение эргономических показателей машин (повышение комфортности, улучшение условий труда и безопасности машиниста, использование подрессоренных и шумопоглощающих кабин и т. д.).
Техническая производительность бульдозера при резании и перемещении грунта Пт м³/ч, определяется по формуле
Пт = 3600Vгрkуkн / Tц
Vгр - геометрический объем призмы волочения, м; kу - коэффициент, учитывающий влияние уклона местности на производительность (при работе на подъемах от 5 до 15% k уменьшается от 0,67 до 0,4; при работе на уклонах от 5 до k увеличивается с 1,35 до 2,25); kн - коэффициент наполнения геометрического объема призмы волочения грунтом, k= 0,85 1,05; Tц - продолжительность цикла, с.
Объем призмы волочения
Vгр = LH2kн / 2tgФkр
L, Н - соответственно длина и высота отвала, м;
Ф - угол естественного откоса грунта в движении, = 20 50;
kр - коэффициент разрыхления грунта.
Продолжительность цикла Тц, с, составляет
Тц = Lp/Vp + Ln/Vn + Lo/Vo + tn
Lp, Ln, Lo - длина соответственно участков резания, перемещения грунта и обратного хода бульдозера, м,
Lp = Vпр/S
S - площадь срезаемого слоя грунта, м², S = Lc (с - средняя толщина срезаемого слоя, м);
Vр, Vn, Vo - скорости бульдозера при резани перемещении грунта и обратном ходе соответственно,
tn - время на переключение передач во время цикла, с, tn от 15 до 20.
Грунт режут на низшей передаче со скоростью 2,5-4,5 км/ч, перемещают со скоростью 4,5-6 км/ч
Техническая производительность бульдозера с поворотным отвалом при выполнении планировочных работ Пт, м³/ч будет
Пт = 3600L(LsinQ - 0,5) / n(L/v + tn)
L - длина планируемого участка, м; Q - угол установки отвала в плане, град; 0,5 - величина перекрытия проходов, м; n - число проходов по одному месту; v - скорость движения бульдозера, м/с.
Скреперы
Это землеройно-транспортные машины, предназначенные для послойной разработки грунтов до I категории включительно (грунты III и IV категорий после предварительного разрыхления), перемещения грунта, из забоя в отвал и отсыпки в отвале слоями заданной толщины. Дальность рационального перемещения грунта составляет 0,5 - 1 км для прицепных и 1,5 - 3 км для самоходных скреперов.Скреперы классифицируют по способу агрегатирования с тягачом, загрузки ковша, выгрузки грунта из ковша.
По способу агрегатирования скреперы делятся на самоходные полуприцепные и прицепные.
Самоходные скреперы имеют собственную силовую установку, обеспечивающую передвижение машины и управление рабочим органами. Для самоходных скреперов используют одноосный колесный тягач.
Полуприцепные скреперы характеризуются тем, что в качестве тягача используется двухосный колесный трактор. Они по своим параметрам (транспортная скорость, дальность транспортирования) не отличаются от самоходных скреперов.
Прицепные скреперы агрегатируют с гусеничными тракторами Ковш прицепного скрепера опирается на две собственные оси так, что нагрузка, в том числе от силы тяжести грунта в ковше, передается на опорную поверх через колеса скрепера.
По способу загрузки различают скреперы, загружаемые подпором грунта, создаваемым за счет тягового усилия, и скреперы загружаемые при помощи специальных загрузочных устройств - элеваторов (элеваторная загрузка).
По способу выгрузки грунта из ковша различают скреперы со свободной разгрузкой путем опрокидывания ковша и высыпания грунта под действием сил тяжести, с принудительной разгрузкой путем перемещения задней стенки при поднятой заслонке и с полупринудительной разгрузкой путем опрокидывания вперед задней стенки и днища ковша, выполненных в виде единого сварного узла.
Наиболее широкое распространение получили самоходные двухосные одномоторные скреперы с одной ведущей осью и загрузкой за счет тягового усилия ввиду простоты конструкции меньшей стоимости по сравнению с другими типами самоходных скреперов. Особенность эксплуатации таких скреперов - необходимость использования толкача при загрузке. Несмотря на дополнительные затраты на содержание толкача (бульдозер с коротким отвалом) и некоторые потери времени на его ожидание, одномоторный самоходный скрепер эффективен при разработке связных грунтов с транспортированием на расстояние до 2200 - 2500 м по трассам с подъемами до 6%.
Конструктивная схема прицепного скрепера приведена на рис. 5.
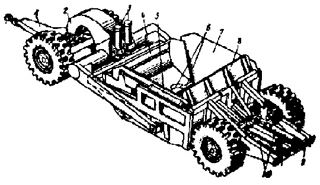
Рис.5. Прицепной скрепер с принудительной разгрузкой
1 - дышло; 2 - тяговая рама; 3 - гидроцилиндры подъема ковша; 4 - передняя заслонка; 5 - гидроцилиндры подъема заслонки; 6 - ножи; 7 - боковые стенки ковша; 8 - задняя подвижная стенка ковша; 9 - буфер; 10 - гидроцилиндры выдвижения задней стенки
Выпускаемые отечественной промышленностью скреперы представляют собой конструктивно-подобный типоразмерный ряд с ковшом вместимостью 4,5-25 м³.
Основным узлом скрепера является ковш, состоящий из днища, боковых стенок 7, передней заслонки 4 и задней стенки 8. Он служит емкостью для разрабатываемого, грунта и является несущей рамой машины, воспринимающей весовые и тяговые на грузки, возникающие при работе скрепера. Боковые стенки и днище выполнены как одно целое. Для обеспечения необходимой прочности и жесткости ковша боковые стенки с наружной стороны имеют усиление в виде коробок жесткости. В передней части днища на подножевой плите установлены ножи 6 пластинчатого типа. У них может быть полукруглая или ступенчатая форма режущей кромки, за счет этого средней частью ножа срезается стружка большей толщины, что улучшает процесс наполнения ковша.
Ковш упряжными шарнирами соединен с тяговой рамой 2, которая шаровой опорой связана с передней осью. Ковш с тягачом сопрягается при помощи дышла 1.
Для обеспечения совместной работы скрепера с толкачом в конструкции предусмотрено буферное устройство 9, к которому прикреплена задняя ось с колесам.
Привод всех элементов рабочего оборудования осуществляется гидроцилиндрами (3 - подъема и опускания ковша, 5 - привода подъемной заслонки, 10 - выдвижения задней стенки), для чего используется гидросистема трактора, в частности насос, распределительная и предохранительно-регулирующая аппаратура. Для того чтобы груженый ковш при транспортировании грунта не мог самопроизвольно опуститься, он фиксируется в поднятом положении специальными замковыми устройствами.
Самоходный скрепер (рис. 6) конструктивно выполнен так же, как и прицепной, за исключением того, что тяговая рама 1 заканчивается хоботом, опирающимся на опорно-сцепное устройство 2 одноосного тягача 3. На ведущей оси тягача смонтированы двигатель с трансмиссией, кабина управления, гидросистема и система управления.
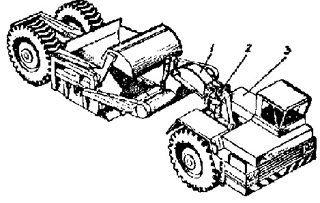
Рис.6. Самоходный одномоторный скрепер
1 - тяговая рама; 2 - опорно-сцепное устройство; 3 - одноосный тягач
Опорно-сцепное устройство позволяет осуществлять поворот тягача относительно ковша на угол 90° в плане и на угол 15° в продольном направлении. Это обеспечивает высокую маневренность скрепера при значительных габаритных размерах и хороший контакт всех колес с поверхностью дороги. Для исключения самопроизвольного опускания груженого ковша в гидролинии цилиндров управления ковшом предусмотрен гидрозамок одностороннего действия.
Техническую производительность скрепера Пт, м³/ч определяют по формуле
Пт = 60Vkkn / Тцkр
k - вместимость ковша скрепера, м; kn - коэффициент наполнения ковша, k = 1,15; kр - коэффициент разрыхления грунта, k =1,2; Тц - продолжительность цикла, мин.
Продолжительность цикла Т мин, составляет
Тц = 0,06(l1/v1 + l2/v2 + l3/v3 + l4/v4) + (tс + tn + 2tпов)
l1, v1 - путь набора грунта и скорость скрепера при копании; l2, v2 - путь и скорость скрепера при разгрузке; l3, v3 - путь и скорость движения груженого скрепера; l4, v4 - путь и скорость порожнего скрепера; tc - время стыковки толкача, tc от 0,4 до 0,5 мин; tn - время переключения передач, tn от 0,5 до 0,1 мин; tпов - время поворота скрепера, tпов от 0,2 до 0,3 мин.
В будущем большую долю скреперного парка составят скреперы с принудительной загрузкой грунта (элеваторной или шнековой). Дальнейшее развитие получат самоходные скреперы с активной задней осью, приводимой от дополнительного двигателя. Произойдет увеличение единичной вместимости ковша до 40 м³ хотя основной парк будет состоять из машин с вместимостью ковша 10 - 18 м улучшатся условия труда машиниста за счет внедрения автоматических систем управления и контроля, созданных на основе микропроцессорной техники; повысится комфорт кабин управления за счет снижения вибрационных нагрузок, установки кондиционеров и других элементов, улучшающих эргономические показатели машин.
Автогрейдеры
Предназначены для планировочных и профилировочных работ при строительстве дорог, аэродромов и других линейно протяженных или имеющих большую площадь объектов. Они также широко применяются при возведении дорожного полотна, устройстве дорожных оснований, при ремонте и содержании дорог, зачистке и планировании откосов, насыпей и выемок.Автогрейдеры классифицируют по мощности установленного двигателя и колесной формуле.
По мощности установленного двигателя автогрейдеры делят на три класса: класс 100 - мощность двигателя 66 - 88 кВт; класс 160 - мощность двигателя 99 - 147 кВт; класс 250 - мощность двигателя 17б-220 кВт.
Колесная формула выражается сочетанием АхБхВ, где А - число осей с управляемыми колеса; Б - число осей с ведущими колесами; В - общее число осей. Колесная формула автогрейдеров классов 100 и 160 выражается соотношением 1х2Х3, а класса 250-1ХЗХЗ.
Современные автогрейдеры (рис.7) выполнены по единой принципиальной схеме в виде самоходных трехосных машин с полноповоротным отвалом и гидравлическим приводом рабочего оборудования.
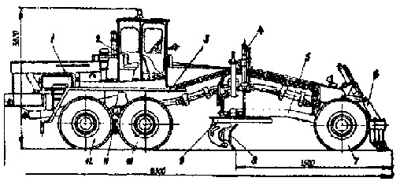
Рис.7. Автогрейдер
1 - силовая установка; 2 - кабина; 3 - рама; 4 - гидросистема; 5 - тяговая рама; 6 - кирковщик; 7 - передний ведущий мост; 8 - отвал; 9 - поворотный круг; 10 - средний ведущий мост; 11 - подвеска мостов; 12 - задний ведущий мост
Автогрейдер включает основную раму 3, на которой смонтирована силовая установка 1, кабина управления 2, основное рабочее оборудование, включающее тяговую раму 5 с отвалом 8 и дополнительное оборудование (кирковщик 6 или бульдозерный отвал).
Головная часть основной рамы опирается на передний мост 7, а подмоторная часть рамы - на подвеску 11 среднего 10 и заднего 12 мостов. Подвеска среднего и заднего мостов выполнена в виде продольно системы. Передние колеса автогрейдера могут устанавливаться с наклоном в обе стороны для лучшей устойчивости при работе на косогорах уменьшения радиуса поворота.
Основное рабочее оборудование состоит из тяговой рамы 5 с отвалом и поворотного круга 9. В нижней части отвала расположены сменные двухлезвийные ножи. Тяговая рама в плане имеет А-образную форму. В передней части она шарнирно соединена с оголовком основной рамы, а в задней подвешена на двух гидроцилиндрах 4, обеспечивающих перевод рамы в рабочее и транспортное положение.
Привод рабочего оборудования позволяет поднимать и опускать тяговую раму вместе с отвалом, поворачивать отвал вокруг оси поворотного круга на угол 360°, выносить отвал (до 300- 800 мм) в обе стороны продольной оси машины, допускает перекос отвала в вертикальной плоскости до 18°, боковой вынос тяговой рамы вместе с поворотным кругом и отвалом для планировки откосов, а также совмещение отдельных установок отвала. На последних моделях автогрейдеров применяют шарнирно сочлененную основную раму, что создает ряд технологических преимуществ, расширяющих сферу их применения, повышающих производительность и улучшающих маневренность.
Техническая производительность автогрейдера при резании и перемещении грунта Пт,м³/ч составляет
Пт = 60SL / (L/vp + tp)n
S - площадь сечения стружки, срезаемой за один проход, м² S от 0,05 до 0,12; L - длина захвата, м; vp - средняя рабочая скорость движения автогрейдера, м/мин; n - количество проходов.
В перспективе планируется значительно расширить типоразмерный ряд автогрейдеров как в сторону увеличения установленной мощности двигателя, так и серийного создания микроавтогрейдеров для коммунальных служб, опытные образцы которых прошли успешное испытание.
Наряду с эти будет продолжено совершенствование существующих машин в направлении повышения комфортности условий труда, создания систем защиты оператора, от опрокидывания, внедрения микропроцессорного управления и т. д.
Машины и оборудование для гидромеханизации
Гидромеханизация в строительстве - это такой способ производства работ и добычи строительных материалов, при котором все операции технологического процесса выполняются за счет использования энергии воды. Гидромеханизация обеспечивает комплексное производство работ: отделение частиц грунта от массива и образование механической смеси грунта с водой (пульпы), транспортирование пульпы к месту укладки грунта, укладку и уплотнение грунта в сооружении или подачу его в отвал.Основными средствами гидромеханизации являются гидромониторы и землесосные снаряды. В промышленном, гражданском и военном строительстве оборудование для гидромеханизации широкого применения не получило.
Машины для уплотнения грунтов
Грунты, разработанные землеройными и землеройно-транспортными машинами, при укладке в насыпи земляных сооружений не обладают достаточной несущей способностью, имеют повышенную фильтрационную способность и характеризуются большой объемной сжимаемостью. Для устранения указанных недостатков грунты искусственно уплотняют до требуемого состояния, характеризуемого коэффициентом уплотнения k значение которого устанавливается строительными нормами в зависимости от вида сооружения и климатических зон.k = Yc / Ycmax
Yc, Ycmax - плотность сухого грунта, максимальная стандартная плотность грунта при оптимальной влажности соответственно:
k от 0,95 до 0,98 - для дорог с усовершенствованным покрытием; k от 0,90 до 0,95 - для дорог с покрытием переходного типа; k от 0,97 до 1,00 - для гидротехнических земляных сооружений; k от 0,80 до 0,90 - для насыпей железных дорог; k от 0,98 до 1,02 - для аэродромов.
В современном строительстве сооружений из отсыпанного грунта применяют следующие способы его уплотнения:
укатка (катки статического действия с гладкими, кулачковыми, решетчатыми вальцами и катки на пневмошинах);
трамбование (трамбующие машины и трамбующие плиты на базе экскаваторов);
вибрационное уплотнение (прицепные и самоходные виброкатки, виброплиты и навесные виброуплотнители).
Катки
Относятся к числу наиболее производительных и дешевых средств. Помимо грунтов они могут быть использованы для уплотнения различных оснований, песчано-гравийных подготовок и дорожных покрытий. Конструктивно катки выполняются статического и комбинированного действия. Катки статического действия могут быть гладкими, кулачковыми, сегментными, решетчатыми и пневмоколесными. По способу агрегатирования катки разделяют на прицепные, полуприцепные и самоходные.Самоходные и прицепные катки статического действия с гладкими металлическими вальцами могут производить послойное уплотнение грунтов на глубину 10 - 15 см.
Самоходные катки с гладкими вальцами применяются все реже. Их вытесняют вибрационные катки комбинированного действия.
Рабочий орган прицепного катка выполнен в виде металлического колеса с жестким ободом. Валец вращается на оси, установленной в цапфах охватывающей рамы. Рама снабжена дышлом с серьгой для соединения с базовым тягачом. На ободе вальца размещен закрытый крышкой люк, через который внутренняя полость вальца может заполняться балластом для увеличения массы катка. В качестве балласта применяют песок или каменные материалы. Поверхность пальца очищается от налипающего грунта скребком, установленным на раме.
Для послойного уплотнения насыпных грунтов используют сцепки из трех-пяти катков. Требуемая степень уплотнения грунта достигается многократным последовательным проходом катка по одному месту.
Наименьшая технологически возможная длина уплотняемого участка зависит от допускаемого времени на разворот в конце участка и при скорости движения катка 1 - 1,5 м/с составляет 200 - 450 м.
Кулачковые катки предназначены для уплотнения тяжелых связных глинистых (нелипких) грунтов, но не дают никакого эффекта при уплотнении несвязных грунтов, так как вследствие высокого давления под кулачками грунт выдавливается в стороны и вверх. У них суммарная опорная поверхность кулачков не превышает 4 - 5% поверхности цилиндра, описанного по вершинам кулачков. Процесс уплотнения грунта распространяется снизу вверх. После первых проходов катка образуются отдельные уплотненные ядра, число которых растет с каждым проходом. Несущая способность грунта увеличивается и каток постепенно поднимается вверх. Для уплотнения верхнего слоя грунта нужны другие катки (с гладкими вальцами, пневмоколесные и другие, способные обеспечить необходимое качество поверхности).
Кулачковый каток (рис.8) состоит из металлического вальца 4 с кулачками 3, рамы 5 со скребками 6 и двух дышел со сцепными устройствами.
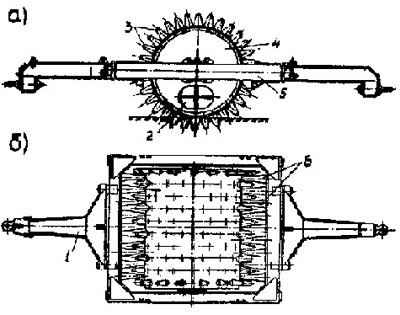
Рис.8. Прицепной кулачковый статический каток
а - вид сбоку; б - вид сверху; 1 - дышло; 2 - люк для загрузки балласта; 3 - кулачки; 4 - валец; 5 - рама; 6 - скребки
Валец с кулачками является рабочим органом катка. Внутренняя полость вальца может заполняться балластом через люк 2. Кулачки к поверхности вальца приварены в шахматном порядке. Ось вальца установлена на подшипниках в охватывающей раме.
Дышла катка имеют петли для соединения с тягачом или друг с другом при работе в сцепке.
Сегментные катки - это разновидность кулачковых катков. Конструктивные отличия сегментных катков сводятся к тому, что вместо кулачков на стальном вальце шарнирно прикреплены специальной формы сегменты. Опорная поверхность у катков увеличена, а шарнирное крепление сегментов обеспечивает более равномерное нагружение грунта, уплотнение которого происходит сверху вниз, как у гладких катков, но более эффективно благодаря пластическому течению грунта из-под сегментов в зазоры между ними. Поскольку затруднена очистка сегментов от налипшего грунта, механизм поворота сегментов блокируется и каток начинает работать как гладкий увеличенного диаметра, что снижает контактное давление. Этот недостаток ограничивает распространение сегментных катков.
Решетчатые катки выполнены в виде плетеной сварной решетки, укрепленной на бортовых и средних кольцах. Внутри решетчатого вальца установлены два конуса, соединенные в середине основаниями, для очистки полости вальца от проваливших через ячейки решетки комьев грунта.
Решетчатые катки хорошо зарекомендовали себя при уплотнении связных и малосвязных грунтов с большим содержанием крупнообломочных включений. Их можно применять и зимой, так как решетки дробят комья и погружают их в массив грунта.
Катки малоэффективны при уплотнении переувлажненных связных грунтов, особенно в зимний период, поскольку грунт интенсивно смерзается с решеткой.
Пневмоколесные катки предназначены для послойного уплотнения грунтов и гравийно-щебеночных материалов в различных областях строительства при широком фронте работ. Они получили широкое распространение благодаря высокой уплотняющей способности и возможности регулировать силовое воздействие на уплотняемые материалы путем автоматического изменения давления в шинах или установки пригруза.
Каток (рис.9) состоит из пяти секций 6. Боковые (крайние) секции катка, соединенные при помощи передней и задней балок рамы между собой, образуют жесткую раму 3. Три средние секции внутри рамы шарнирно крепятся к передней балке рамы. Это позволяет им независимо перемещаться в вертикальной плоскости. Массу катка увеличивают путем загрузки балласта в бункеры секций 4. Выгрузка балласта производится через люки в днище бункеров. Рама катка при помощи опорно-поворотного устройства (дышла) 2 соединяется с одноосным тягачом 1.
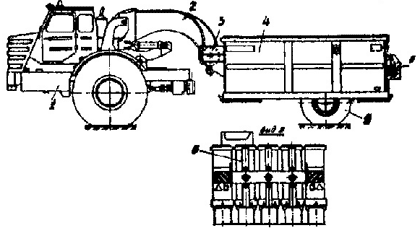
Рис.9. Пневмоколесный каток прицепной
1 - тягач; 2 - дышло; 3 - рама; 4 - бункер для загрузки балласта; 5 - пневмоколесо; 6 - секция катка
Колеса крайних секций оснащены пневмотормозами. В процессе работы давление в пневмоколесах 5 может регулироваться из кабины тягача.
Все рассмотренные типы катков (за исключением пневмоколесного) для повышения эффективности могут оснащаться встроенными вибровозбудителями. Привод вибровозбудителя может осуществляться от индивидуального двигателя или от вала от бора мощности базовой машины через клиноременную передачу. Раму и двигатель от вибрации защищают с помощью резинометаллических амортизаторов. Вибровозбудитель включается и выключается по мере необходимости при помощи управляемой муфты.
Самоходные вибрационные катки комбинированного действия предназначены для уплотнения насыпных и предварительно спланированных слоев грунта, нижних слоев асфальтобетонных покрытий и материалов дорожных оснований. В последнее время они получили широкое распространение.
Высокий уплотняющий эффект катков этого типа обусловлен совместным воздействием металлического вибровальца и ряда пригруженных пневмоколес.
Каток (рис. 10) состоит из силового модуля 1 и шарнирно сочлененного с ним вибровальца 2 с полурамой 5. Шарнирное сочленение 6 обеспечивает возможность поворота полурамам силового модуля и вибровальца в горизонтальной плоскости и относительно вертикальной оси. Поворот в горизонтальной плоскости осуществляется при помощи двух гидроцилиндров 7. Смачивание вальца специальной эмульсией, поступающей из емкости 4, предотвращает налипание на валец частиц уплотняемого материала.
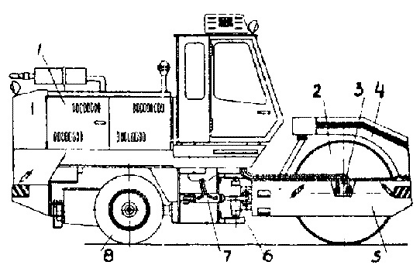
Рис.10. Самоходный вибрационный каток комбинированного действия
1 - силовой модуль; 2 - вибровалец; 3 - гидромотор привода вибровозбудителя; 4 - бак смачивающей системы; 5 - полурама вибровальца; 6 - шарнирное сочленение полурам; 7 - гидроцилиндр поворота катка; 8 - пневмоколесо
Силовой модуль включает двигатель внутреннего сгорания, насосную станцию, кабину оператора с системой управления катком и пневмоколесную ходовую часть 8. У катка гидрообъемная трансмиссия привода вибровальца и передвижения. Для защиты машиниста и рамы катка от вибрации вибровалец устанавливают на резинометаллических амортизаторах.
Такую конструктивно-компоновочную схему имеют большинство выпускаемых в настоящее время самоходных виброкатков комбинированного действия.
Трамбующие машины с падающими плитами
Предназначены для уплотнения тяжелых связных грунтов, отсыпаемых толщиной 0,8 м и более при сосредоточенных объемах работ, а также в гидротехническом строительстве. Высокий уплотняющий эффект обусловлен высокой энергоотдачей (18835 Дж от единичного удара плитой).Трамбующая машина (рис. 11) представляет собой навесное рабочее оборудование на базе гусеничного трактора (Т-130.1.Г, Т-170.01), оборудованного ходоуменьшителем.
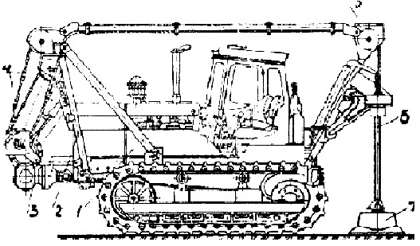
Рис.11. Трамбующая машина с падающими плитами
1 - гусеничный трактор; 2 - передняя подвеска; 3 - редуктор привода плит; 4 - кривошипно-полиспастный механизм привода плит; 5 - задняя подвеска; 6 - направляющие штанги; 7 - трамбующие плиты
Оборудование для трамбования содержит переднюю подвеску 2 с редуктором 3 и блоками кривошипно-полиспастного механизма 4 привода плит и заднюю подвеску 5 с блоками, направляющими штангами 6 и подвешенными на канатах трамбующими плитами 7.
Конструкция кривошипно-полиспастного механизма привода плит обеспечивает поочередный подъем в сброс обеих плит, выбор слабины каната перед подъемом, а также свободное падение плит с учетом осадки грунта. Направляющие трамбующих плит заделаны в траверсе задней подвески при помощи резиновых амортизаторов и имеют управляемые из кабины удлинители.
Виброплиты
Используют при уплотнении грунта в стесненных условиях (пазухи фундаментов, вокруг колонн в опор, при устройстве грунтовых подсыпок под полы зданий и т. д.).В качестве привода виброплит применяют трехфазные асинхронные двигатели в двигатели внутреннего сгорания.
Существует несколько вариантов исполнения виброплит, но наиболее широкое распространение получили подвесные одно- и двухмассные виброплиты, самопередвигающиеся виброплиты.
Самопередвигающиеся виброплиты (рис.12) характеризуются тем, что у них источник направленных колебаний представляет собой дебалансный вибровозбудитель. Самопередвижение плиты осуществляется под действием горизонтальной составляющей суммарной вынуждающей силы, генерируемой вибровозбудителем.
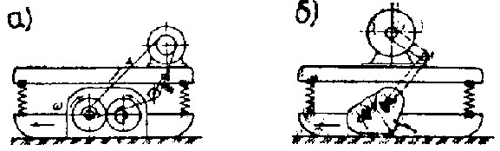
Рис.12. Виброплита самопередвигающаяся
а - с реверсивным механизмом; б - с наклоняющимся вибровозбудителем
Горизонтальная составляющая может возникать при повороте одного дебаланса относительно другого (рис.12, а) или при наклоне корпуса вибровозбудителя (рис.12, б) относительно основания при помощи регулировочных тяг
Производительность изготавливаемых виброплит составляет 300-900 м²/ч при массе от 150 до 1400 кг. Глубина уплотнения грунта достигает 0,3-1 м.
Техническую производительность грунтоуплотняющих машин и оборудования непрерывного действия Пт, м²/ч определяют по объему уплотненного грунта:
Пт = 1000(B - d)hv / n
В - ширина полосы уплотнения, принимаемая равной ширине катка, сцепа, виброплиты, трамбующей машины, м; b - ширина перекрытия смежных полос, b от 0,1 до 0,15 м; h - толщина слоя эффективного уплотнения, указываемая в характеристике уплотняющего оборудования, м; v - средняя рабочая скорость передвижения машины (оборудования), км/ч; n - необходимое число проходов по одному месту.
Бурильные машины и оборудование
Бурильные машины в строительстве применяют для бурения скважин под установку опор линий электропередач и связи, столбов дорожных указателей и ограждений, устройства буронабивных свай под фундаменты зданий и сооружений, опор мостов, производства буровзрывных работ и т. д. Машины для буровзрывных работ относятся к горным машинам.Наибольшее распространение в строительстве получили бурильно-крановые машины.
Бурильно-крановой называется самоходная машина, имеющая бурильное и крановое оборудование, предназначенное для бурения скважин и установки в них различных элементов строительных конструкций.
Бурильно-крановая машина (рис. 13) состоит из базовой машины 8, навесного бурового и кранового оборудования.
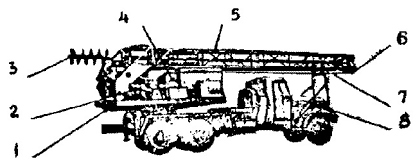
Рис.13. Бурильно-крановая машина БМ-802С
1 - поворотная платформа; 2 - гидроцилиндры перевода рабочего органа из рабочего в транспортное положение; 3 - бур; 4 - крановая лебедка; 5 - мачта; 6 - блоки; 7 - канаты; 8 - базовая машина
Рабочий орган - бур 3 - располагается на мачте 5, которая переводится из транспортного горизонтального в рабочее вертикальное положение гидроцилиндрами 2.
Все рабочее оборудование размещено на поворотной платформе 1, что позволяет бурить по окружности без дополнительной перестановки машины.
Сменный шнековый бур имеет режущие кромки из твердого сплава. Вращается бур от двигателя через механическую трансмиссию с несколькими скоростями в одну или другую сторону.
Вверх и вниз бур перемещается при помощи гидроцилиндров, позволяющих также создавать принудительный напор на бур при бурении.
Крановое оборудование включает крановую лебедку 4, расположенную на поворотной платформе, систему канатов 7 и блоков 6, грузозахватное устройство. Крановая лебедка также имеет привод от двигателя через механическую трансмиссию.
В зависимости от типа базовой машины бурильно-крановые машины делятся на автомобильные (рис. 13) и тракторные на гусеничных и пневмоколесных (рис. 14) тракторах.
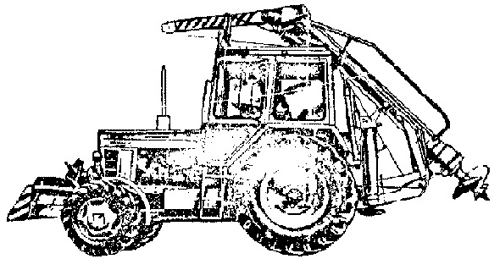
Рис.14. Машина бурильно-крановая БМ-205Б
По типу привода различают бурильные машины с гидравлическим и механическим приводом.
По глубине бурения выпускаются машины для бурения скважин глубиной 2, 3 и 8 м при диаметре скважин от 0,3 до 0,8 м.
Индексы бурильно-крановых машин состоят из букв и цифр. Например, БМ-802С означает: бурильно-крановая машина с глубиной бурения до 8 м, вторая модель, модернизация "С".
В последнее время бурильное оборудование, предназначенное для выполнения работ небольшого объема, широко применяется в качестве сменного рабочего оборудования на различных строительных машинах: одноковшовых экскаваторах, многоцелевых погрузчиках (рис. 15) и т. д.
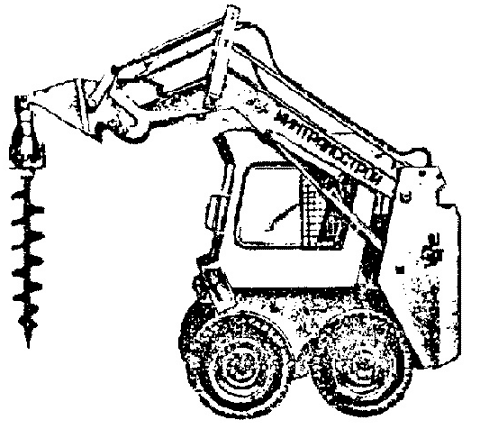
Рис.15. Сменное бурильное оборудование на многоцелевом малогабаритном погрузчике